How Can I Tell If My Alternator Is Bad?
Your car’s electrical system depends on a properly functioning alternator to keep everything running smoothly. When this critical component starts failing, you’ll notice warning signs that shouldn’t be ignored. Recognizing these symptoms early can save you from being stranded with a dead battery and expensive repair bills.
What Does Your Alternator Actually Do?
The alternator serves as your vehicle’s power generator while the engine runs. This essential component converts mechanical energy from the engine into electrical energy, charging your battery and powering all electrical systems. Without a working alternator, your car relies solely on battery power, which drains quickly.
Most modern alternators produce between 13.5 to 14.5 volts when operating correctly. This voltage level ensures your battery stays charged while supporting headlights, air conditioning, radio, and computer systems. The alternator also maintains consistent voltage output regardless of engine speed, thanks to built-in voltage regulators.
Warning Signs Your Alternator Needs Attention
Dashboard Warning Light Activation
Your dashboard battery light represents the most obvious indicator of alternator problems. This red or amber symbol typically resembles a battery or displays “ALT” or “GEN.” When illuminated, the light signals that your charging system isn’t working properly.
Don’t assume the battery light only indicates battery problems. The charging system warning light activates whenever voltage drops below normal operating levels. This drop usually stems from alternator failure rather than battery issues.
Dimming or Flickering Headlights
Headlights that dim or flicker while driving point directly to alternator troubles. You’ll notice this symptom most clearly during nighttime driving or in dark parking areas. The lights may brighten when you rev the engine, then dim again at idle.
Interior lights also exhibit similar behavior when the alternator struggles. Dashboard illumination, dome lights, and instrument panel backlighting may fade or pulse rhythmically. These electrical fluctuations indicate inconsistent power generation from your failing alternator.
Strange Electrical Behavior
Electrical components throughout your vehicle depend on steady voltage from the alternator. When this component fails, you’ll experience erratic behavior from various systems. Windows may move slowly, power seats respond sluggishly, and the radio might cut in and out.
Modern vehicles with extensive computer systems show even more dramatic symptoms. Engine management systems, transmission controls, and safety features may malfunction or trigger error codes. These electronic glitches often worsen progressively as the alternator deteriorates.
Unusual Sounds From the Engine Bay
A failing alternator often produces distinctive noises that alert attentive drivers. Grinding sounds typically indicate worn internal bearings that need immediate attention. Whining or squealing noises usually point to belt problems affecting alternator operation.
Bearing failure creates a rough, gravelly sound that increases with engine speed. This noise originates from the alternator’s location and becomes more pronounced under electrical load. Ignoring these sounds leads to complete alternator failure and potential engine damage.
Dead Battery Despite Recent Replacement
A new battery that repeatedly dies suggests alternator problems rather than battery defects. The alternator must recharge the battery during operation, replacing power used by electrical systems. Without proper charging, even new batteries drain completely.
Jump-starting becomes a temporary solution when the alternator fails. Your car may start and run briefly after jumping, but the engine dies once you remove the jumper cables. This pattern clearly indicates charging system failure.
Burning Smell or Visible Damage
Overheating alternators produce distinctive burning odors that smell like hot metal or electrical components. These smells often accompany visible damage such as melted wiring, burned connectors, or discolored alternator housing.
Electrical fires represent serious safety hazards that require immediate attention. Pull over safely and shut off the engine if you detect burning smells or see smoke from the alternator area. Never ignore these warning signs.
How to Test Your Alternator
Visual Inspection Methods
Start your alternator diagnosis with a thorough visual examination. Look for obvious signs of damage including cracked housing, loose connections, or corroded terminals. Check the drive belt for proper tension, cracks, or glazing that affects alternator operation.
Inspect wiring harnesses connected to the alternator for damage, corrosion, or loose connections. Poor electrical connections create resistance that mimics alternator failure symptoms. Clean corroded terminals and tighten loose connections before assuming alternator replacement is necessary.
Voltage Testing Procedures
Digital multimeters provide accurate alternator performance measurements that confirm your diagnosis. Set your multimeter to DC voltage and connect the leads to your battery terminals. Record the voltage reading with the engine off, which should measure around 12.6 volts for a healthy battery.
Start the engine and observe the voltage reading while idling. A properly functioning alternator produces between 13.5 and 14.5 volts at idle speed. Rev the engine to approximately 2,000 RPM and verify the voltage remains within this range without excessive fluctuation.
Turn on electrical accessories like headlights, air conditioning, and radio while monitoring voltage output. The alternator should maintain proper voltage levels even under heavy electrical load. Voltage drops below 13 volts indicate alternator weakness or failure.
Load Testing Your Charging System
Professional-grade load testers provide comprehensive alternator evaluation beyond simple voltage measurements. These devices apply controlled electrical loads while measuring alternator output capacity. Most auto parts stores perform free alternator testing using professional equipment.
Load testing reveals alternator problems that don’t appear during basic voltage testing. An alternator might produce correct voltage at light loads but fail under heavy electrical demand. This condition causes intermittent problems that are difficult to diagnose without proper testing.
Common Alternator Failure Causes
Normal Wear and Age
Alternators contain moving parts that wear naturally over time and mileage. Internal brushes make physical contact with slip rings, gradually wearing down through normal operation. Most alternators last between 80,000 and 150,000 miles depending on driving conditions and maintenance.
Bearing wear represents another common age-related failure mode. Alternator bearings support the rotor shaft and enable smooth rotation. Contamination, lack of lubrication, or excessive tension accelerates bearing wear and causes premature failure.
Environmental Damage
Extreme temperatures affect alternator performance and longevity significantly. Excessive heat from engine bay conditions or external sources damages internal components and insulation. Cold temperatures increase electrical resistance and place additional stress on the charging system.
Water damage from flooding, pressure washing, or driving through deep puddles can destroy alternator electronics instantly. Salt exposure from winter road treatments accelerates corrosion and electrical connection problems. Regular cleaning helps prevent environmental damage accumulation.
Electrical System Problems
Voltage regulator failure causes alternator overcharging or undercharging conditions that damage both components. Modern alternators integrate voltage regulators internally, making replacement more complex and expensive than older external regulator designs.
Short circuits in electrical accessories create excessive current draw that overloads alternator capacity. This condition generates excessive heat and accelerates component wear. Faulty wiring, damaged connectors, or aftermarket electrical installations often cause these problems.
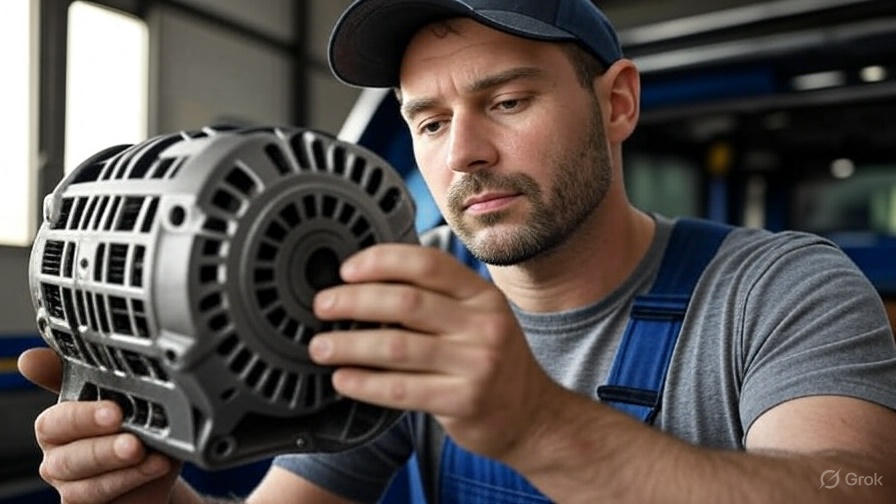
Professional Diagnosis vs DIY Testing
When to Seek Professional Help
Complex electrical problems require professional diagnostic equipment and expertise that exceed typical DIY capabilities. Modern vehicles integrate alternator control with engine management systems, making diagnosis more challenging for amateur mechanics.
Intermittent problems prove particularly difficult to diagnose without specialized equipment. Professional technicians use oscilloscopes and computerized test equipment to identify subtle alternator problems that basic multimeter testing misses.
Cost Considerations for Testing
Professional alternator testing typically costs between $50 and $100 at independent repair shops. Many auto parts retailers offer free testing services when you remove the alternator yourself. This option saves diagnostic fees but requires more labor and time investment.
Consider the value of your time and diagnostic accuracy when choosing between professional and DIY testing approaches. Incorrect diagnosis leads to unnecessary part replacement and additional expense that often exceeds professional testing costs.
Alternator Replacement Timeline
How Long Alternators Typically Last
Most alternators provide reliable service for 7 to 10 years under normal driving conditions. High-mileage vehicles, frequent short trips, and extreme operating conditions reduce alternator lifespan significantly. City driving with frequent stop-and-go conditions places more stress on charging systems than highway driving.
Performance modifications, aftermarket electrical accessories, and sound systems increase alternator workload and accelerate wear. High-output alternators designed for modified vehicles cost more initially but provide better long-term reliability under demanding conditions.
Immediate vs Scheduled Replacement
Complete alternator failure requires immediate attention to prevent being stranded. Partial failure allows some flexibility in scheduling repairs, but delays risk complete system failure at inconvenient times and locations.
Plan alternator replacement during routine maintenance periods when possible. This approach allows time for price comparison, quality part selection, and scheduling with trusted repair facilities. Emergency repairs often cost more and limit your options for parts and service providers.
Prevention and Maintenance Tips
Regular Inspection Practices
Include alternator inspection in your routine maintenance schedule every 6 months or 10,000 miles. Check belt condition, electrical connections, and mounting hardware for signs of wear or damage. Early detection prevents minor problems from becoming major failures.
Keep the alternator area clean and free from debris that restricts airflow and causes overheating. Remove leaves, dirt, and other contamination that accumulates around the alternator housing and cooling fins.
Driving Habits That Extend Life
Avoid excessive electrical loads when the engine idles for extended periods. Air conditioning, heated seats, and high-power audio systems drain alternator capacity at low engine speeds. Rev the engine periodically during extended idling to increase alternator output.
Allow the engine to warm up before applying heavy electrical loads during cold weather. Cold alternators produce reduced output until reaching normal operating temperature. Gradual loading prevents stress and extends component life.
Your alternator plays a crucial role in vehicle reliability and safety. Recognizing failure symptoms early and addressing problems promptly prevents roadside breakdowns and protects other electrical components. Regular maintenance and proper driving habits extend alternator life and reduce replacement costs.
Don’t ignore warning signs or delay necessary repairs. A failing alternator affects your entire electrical system and can leave you stranded without warning. When in doubt, professional testing provides accurate diagnosis and peace of mind for safe, reliable transportation.